Réalisations laser #2 : la micro soudure au service de l’aérospatial
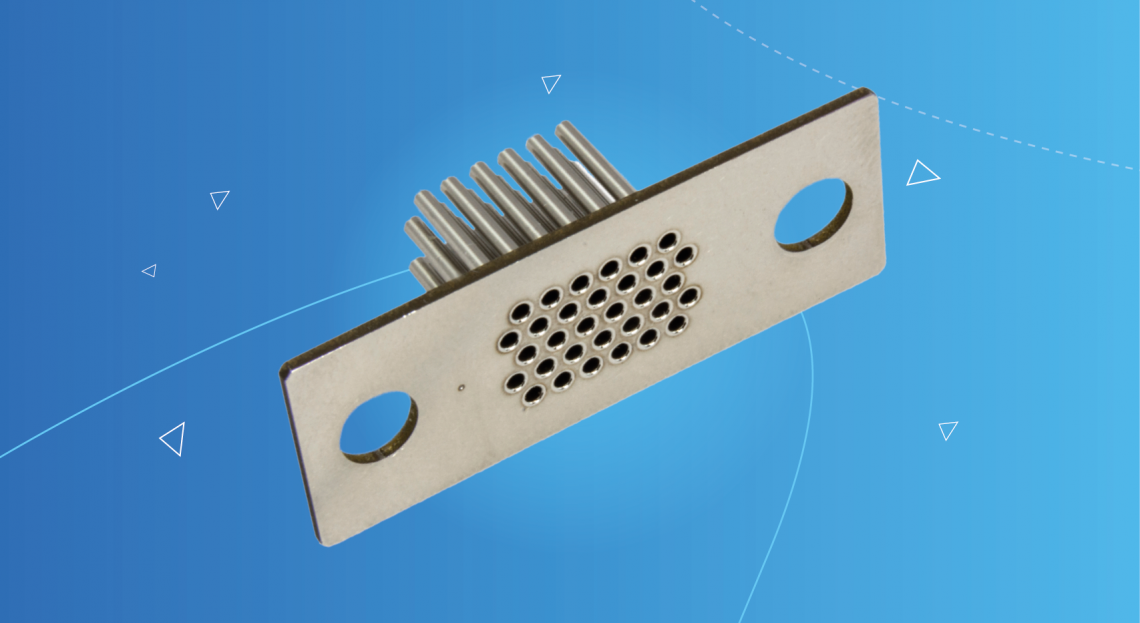
Poursuivons notre exploration des réalisations phares de nos équipes dans le domaine du soudage. Alors après le coude SMA – ou comment le passage du brasage de métaux à la soudure a entraîné une économie significative de 40 % pour notre client –, découvrez dans ce nouvel épisode l’univers ultra précis de la micro soudure pour l’industrie aérospatiale.
Contexte : l’innovation au cœur de l’espace
L’aérospatial, l’aéronautique et l’industrie médicale sont des domaines qui repoussent constamment les limites de la technologie. Pour répondre aux exigences pointues de ces secteurs, des avancées technologiques sont nécessaires. La soudure laser est l’une de ces innovations qui a su apporter des solutions adaptées aux contraintes du secteur spatial.
Elle offre des avantages considérables pour les composants spatiaux et permet de réduire le poids des matériaux, d’assurer la tenue mécanique des systèmes embarqués, de garantir l’étanchéité au vide, et de renforcer la fiabilité des composants. Autant de qualités essentielles pour les voyages dans l’espace, où chaque milligramme compte.
La mission : un échangeur à plaques
Notre défi était de travailler sur un échangeur à plaques, un composant crucial qui permet un échange de chaleur sans contact.
En 2017, notre client français, spécialisé dans la cryogénie, nous a fait confiance pour relever ce défi. Auparavant, cet échangeur était assemblé en Amérique du Nord. Trouver un sous-traitant français pour ce projet de satellite européen de télécommunication était donc une décision stratégique et pleine de sens.
En travaillant ensemble, nous avons pu mettre en avant l’expertise française dans le domaine de la soudure laser et contribuer à un projet spatial d’envergure.
Nos références sur le secteur spatial
|
Les caractéristiques de l’échangeur
L’échangeur à plaques que nous avons travaillé pour notre client français spécialisé dans la cryogénie est un composant complexe et exigeant. Il est de forme cylindrique, avec un diamètre de 60 mm et une longueur de 35 mm ; et les plaques qui le composent ont une épaisseur de seulement 1 mm.
Ce composant est fabriqué en Inox 316L, un acier inoxydable austénitique, connu pour sa résistance à la corrosion et sa grande ductilité.
La pièce est constituée de 100 tubes, chacun d’un diamètre de 1 mm et d’une paroi de seulement 0,1 mm. Chaque tube est espacé de son voisin de 1,5 mm, et doit être soudé un par un.
Une contrainte technique triple
La réalisation de cet échangeur à plaques a été un véritable défi pour nos équipes :
- la taille de l’ensemble : il s’agit bien de micro soudure, ce qui nécessite une grande précision et une technologie adaptée ;
- l’étanchéité de l’échangeur : elle doit permettre d’éviter toute fuite de fluide qui pourrait endommager le composant ou le système dans lequel il est intégré ;
- la résistance à la pression mécanique : la pression du fluide qui traverse l’échangeur s’élève à 70 bars, soit bien plus que la pression en sortie d’un robinet domestique (1 à 3 bars).
« Nos équipes ont d’abord réalisé une éprouvette, c’est-à-dire une pièce présentant les mêmes caractéristiques que la pièce de notre client, afin de choisir la bonne technologie. Sur un tel projet, chaque micro soudure de tube doit être testé pour la résistance mécanique et l’étanchéité. Nous n’avons pas le droit à l’erreur. »
Michel Almuneau, responsable technique chez Laser Rhône Alpes
La mise en œuvre du projet
Devant la complexité des manipulations nécessaires, toutes les expertises du bureau d’études de Laser Rhône Alpes ont été sollicitées.
Étude de faisabilité
La première étape a été l’étude de faisabilité, menée par notre ingénieur méthode. Compte tenu de la taille très petite des pièces en Inox et de la nécessité d’une grande précision, nous avons opté pour une technologie laser à fibre continue de faible puissance.
Positionnement de la pièce et des tubes
En collaboration avec notre concepteur d’outillage, nous avons ensuite dû imaginer comment positionner la pièce et chacun de ses 800 tubes, afin de garantir une soudure sans défaut. Cette étape a nécessité une grande précision et une approche rigoureuse.
Programmation
Nous avons créé un programme de commande numérique du laser, qui nous a permis d’assurer la plus grande précision et de garantir la qualité de notre travail.
Tests et contrôles qualité
Nous avons dû imaginer un protocole de tests pouvant être réalisés sur chacun des 800 tubes de la pièce finale, au fur et à mesure de leur assemblage. Une étape essentielle pour garantir la fiabilité, l’étanchéité et la résistance de l’échangeur à plaques dans des conditions extrêmes.
« L’utilisation d’une caméra permet de vérifier la position de chaque tube avant la soudure. C’est un travail de très grande précision, d’autant que 100 % des tubes sont contrôlés par nos soins. On utilise un jet d’hélium pour garantir l’étanchéité. Le taux de fuite attendu est de 1.10-4 mbar.l/s. L’assemblage d’une pièce nécessite donc environ une journée. »
Michel Almuneau, responsable technique chez Laser Rhône Alpes
La micro soudure laser est une expertise en soi. C’est pourquoi nos équipes participent au salon international Micronora, qui réunit les plus grands professionnels en microtechniques et nanotechnologies, à Besançon tous les 2 ans.

